The ReAvenger Saga
This deals with an unconventional and largely untested
method of multistaging. PLEASE don't consider this method
safe or tested.
Back in the day, around 1972 or so, I bought the
biggest rocket I'd owned so far - the Estes Avenger. It was a two stage rocket and
used the classic Estes staging and mounting method of using cellophane
tape to hold the motors together for staging and masking tape
for the friction fit to hold the motors in place.
I launched it once and it flew well. However, on recovery I discovered
that even though the second stage had lit fine, at separation the first
stage engine broke loose of the first stage leaving the first stage
still attached. The second stage burned normally, but its exhaust
went through the first stage where the motor had just been.
This burned out the engine mount. The top part
was fine, but at the bottom of the first stage, the engine mount was
completely burned away. Luckily, the rocket body was in good shape.
This is the way it sat for years in my parent's attic. During a clean
up they sent the rockets back my way and the Avenger lived in my closet
for several more years. When a launch opportunity approached, I decided
to see if I could resurrect some of the old rockets, including my original
Alpha and the Avenger.
Because of the way the engine had blown out, I was resolved to find a way
to hold the motors better than using masking tape. I also decided since
I was replacing the motor mount, I might as well upgrade to a
D engine mount. I did some fitting and tests and came up with something
that looked like it would work. To compensate for the additional weight
in the rear, I added nose weight in the way of metal washers attached to
the nose cone eyelet.
I first flew it single stage and it flew well, but a fin broke off on recovery
so that was it for that day. About a year later I decided to try a two
stage launch, but with something smaller than a D. In the mean time, I'd
gotten a copy of the G. Harry Stine
Handbock
of Model Rocketry. I'd learned from the chapter on multistaging about the
importance of holding the stages together for a few milliseconds so that the
hot gas and particles of burning fuel could enter the upper stage motor before
the shockwave blew them apart.
The problem here was that I had motor mount clips on both the upper and lower
stage mounts - there was no way to get the tape around the motors and
still assemble the rocket. What to do? I settled on hot glue. I put a good sized ring
of hot glue on the top of the first stage motor, the adapter (since I was using
an 18mm motor in a 24mm mount) and the mount. I was careful to keep the glue away
from the propellent in the first stage. I then assembled the stages quickly
and let the glue set.
Since this was a test, I used as small an engine as I dared (not sure which
one, but most likely a B6-0 - I miss those old B14-0
boosters!). and a small A engine for the upper stage. If it didn't stage, I
didn't want it getting very high.
It staged beautifully, though it appeared the stages held together for a
second or so, the upper stage thrust simply venting through the lower
stage nozzle until the hot glue melted and it released.
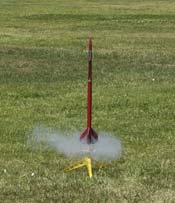
Avenger launch, June 2002 - click for larger image
About a year later at our next launch, June of 2002, I was ready to try
the old Avenger with an Estes D12-0 first stage. This time I used a
bit less hot glue to prevent the delay in separation.
This turned out to be essentially fatal for the rocket. The first stage
portion of the flight went well, but it was obvious right away that the
stages separated before the upper stage lit. The first stage tumbled down
and was soon passed by the upper stage coming straight down. It hit on
reasonably hard ground and pretty much disintegrated.
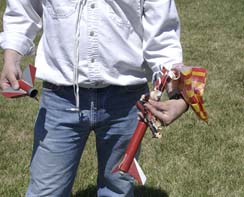
Avenger Aftermath - click for larger image
I decided to see what I could do with the parts that survived. The nose cone was in
surprisingly good shape. The balsa transistion, one of the
fins from the upper stage and the entire lower stage survived (actually,
you can probably see in the photo that two fins survived the landing, but
only one of them survived being removed). Oh, and don't forget
the launch lug.
My construction back when I was 14 or so, was, well, somewhat impatient.
Two not quite matching shades of red had been used, one of which was
house paint, the balsa was not noticably filled and I'd actually
used electrical tape for some details.
I took the surviving pieces, sanded and filled the balsa and replaced
the destroyed pieces - the two pieces of tubing, the upper stage
motor mount (also didn't survive the deconstruction) and two of the upper
stage fins. It came together nicely
and I settled on a fun paint scheme: all new parts were white, the
parts still surviving from the original were red.
I have yet to fly it, but if I do, I'll use more rather than less hot glue,
that's for sure.
NOTE: While hot glue is not hot enough to set off the propellent, using an electrically
heated device near a flammable substance should at least be done carefully. Keep the
metal tip away from the propellent. Keep glue out of the space between the stages
as it could prevent staging.
I cannot recommend this method as I have not
had enough launches to know if it's safe and reliable.
Don't try this unless you're confident that you can deal safely with the
consequences of a failed upper stage ignition as well as the hot glue process.